Groundbreaking textile-to-textile recycling technology for true circularity.
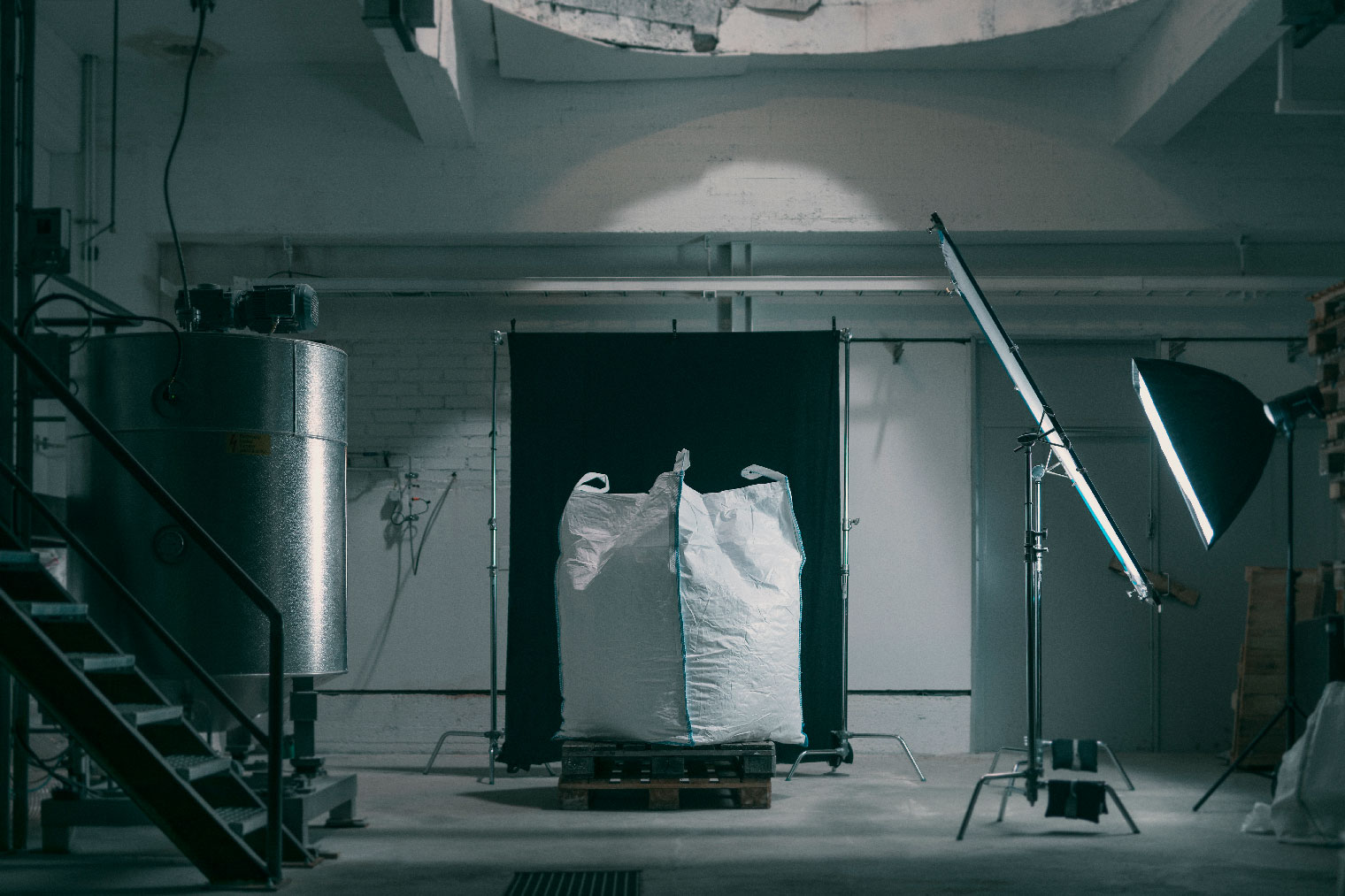
Our patented technology takes piles of textile waste that would otherwise be landfilled or burned and transforms them into brand-new premium-quality fibers for the textile industry.
How it works.
We take in cotton-rich textile waste no longer fit for use and we clean it. It doesn’t matter what color the incoming textiles are, it doesn’t matter how worn out they are, it doesn’t even matter if there’s something synthetic like polyester or elastane in the mix, as long as about 88% of the total is cotton.
During the cleaning phase we remove synthetic fibers and dyes and capture what’s precious to us: the cellulose, a building block all aplants that is most abundant in cotton. We break the cellulose down at the molecular level, activate it with urea and dissolve it to create a liquid cellulose. The liquid cellulose is wet-spun into new fiber filament and cut to staple length, washed and dried.
And voilà, old textiles that were once destined to become pollution have instead become valuable, brand-new textile fibers that are ready to be made into new yarns, fabrics, and textiles. The scientific name of our unique textile fiber is cellulose carbamate fiber – but you can call it Infinna™.
Hover over the images to learn more about our process.
Collection and sorting
Textile waste is collected and sorted by type. For us, the most valuable textiles have a high cotton content.
Disintegration
Non-fibrous materials like buttons, zippers and so on are removed, and the textiles are mechanically disintegrated to fine shreds.
Fiber separation
The cellulose is captured and separated from non-cellulosic particles like polyester and dyes.
Carbamation
The cellulose is activated with urea and a stable, dissolvable cellulose carbamate powder is born. Whether initially a T-shirt, cardboard or rice straw, the raw material turns into the same powder. From this point on material originating from the different feedstock types can be mixed.
Dissolving and wet-spinning
The cellulose powder is turned into a honey-like liquid and impurities are filtered out. New fiber filaments are born when the cellulose crystallizes during the wet spinning process.
Infinna™
The fiber filament is cut, washed and dried. The regenerated cellulose carbamate staple fiber – Infinna™ – is ready for the next phase in the textile manufacturing supply chain.
Delivery
The Infinna™ staple fibers are delivered to yarn spinners or nonwovens manufacturers to be made into products like clothing and home textiles, or wipes and diapers.
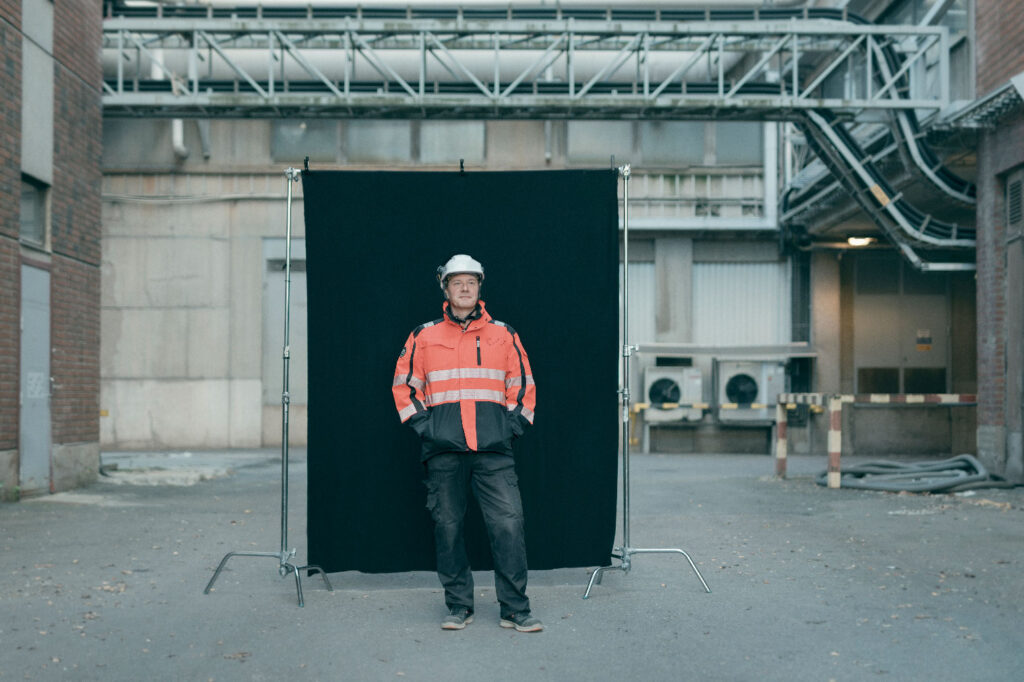
Coming up: Commercial-scale Infinna™ Factory.
And More.
Having produced Infinna™ at our two pilots in since 2018, we are now working to build the first commercial-scale Infinna™ factory with a capacity of 30,000 metric tons of Infinna™ annually, which is equivalent to the fiber needed for about 100 million T-shirts. With most of the future factory´s production capacity already sold out for several years ahead, and the demand for cotton-like recycled fibers by far exceeding the supply in the global market, we are accelerating the Infinna™ capacity build-up by actively advancing the next, larger-capacity Infinna™ factories in close partnerships.
_
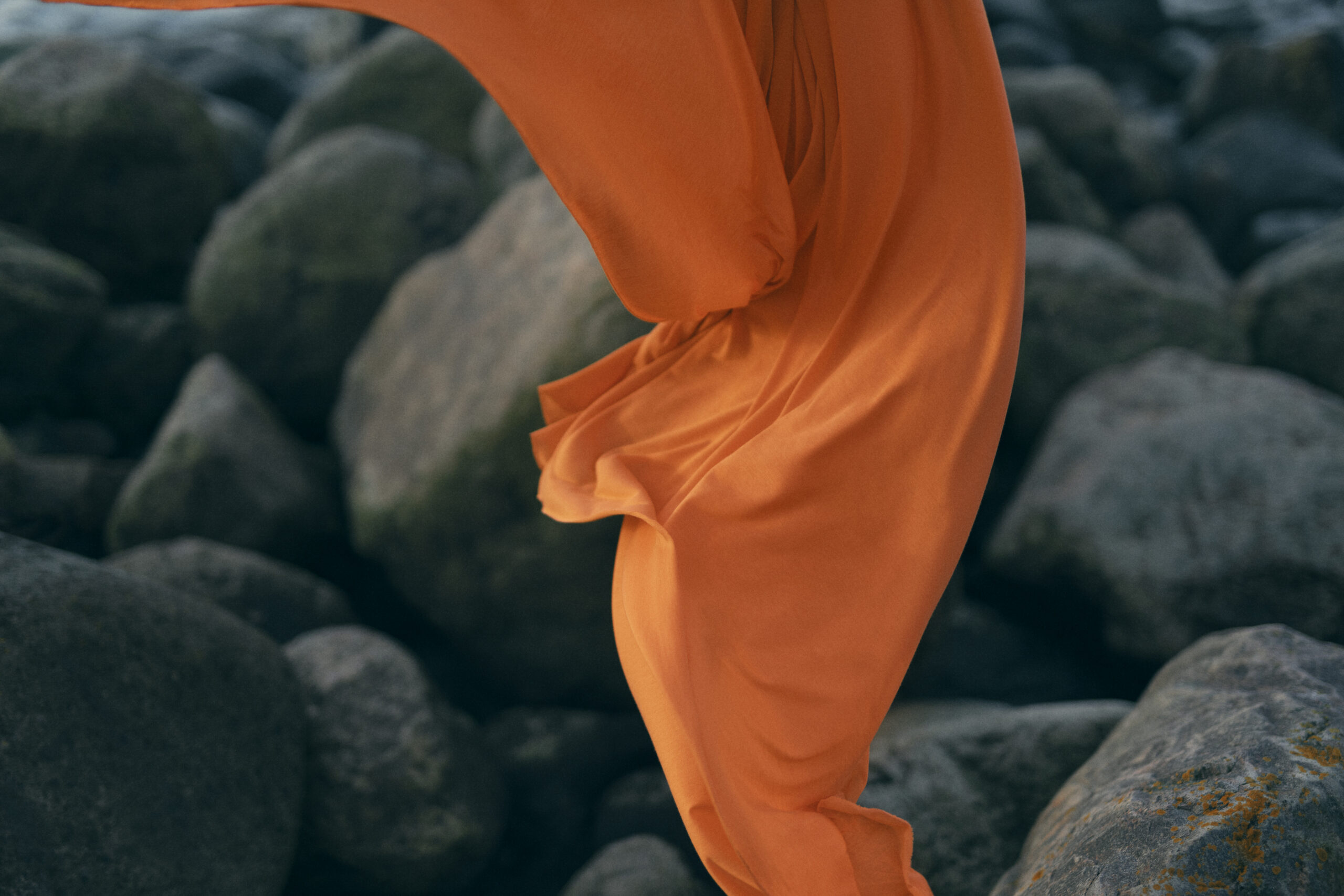
Future-proofed business.
It’s coming – a future where recycled and regenerated textiles replace those made with new resources. Why? Because it’s what people and brands want, the environment needs and future regulation supports. As your partner, we help to future-proof your business through the unique benefits of our ready and proven technology.
New premium product
Enhance your existing product portfolio with Infinna™ – a unique, sustainable, and in-demand premium textile fiber that looks and feels like cotton and is as versatile.
All-in-one process
Our ready and proven technology covers all steps – from the pre-treatment of the raw material to the finished, ready-to-ship regenerated Infinna™ textile fiber with high demand.
Responsible chemistry
Our chemistry conforms to the ZDHC and MRSL and the whole process has been carefully designed to be safe, eliminate waste, and preserve resources.
Circular solution
Replace resource-heavy virgin raw materials that tax biodiversity with cellulose-rich feedstock that’s already in use, like old clothes. Keep biomass in circulation and leave the land for food crops and wilderness.
Endless flexibility
We make Infinna™ 100% from textile waste, but our robust technology could also be utilized to produce the same, high-quality fiber from a wide range of other cellulose-rich feedstock, such as used cardboard, paper, and wheat or rice straw, by amending the production set-up.
Made modular
Our technology is made up of 3 distinct modules that can be located at a single facility or at multiple sites. This opens up possibilities for various new-builds as well as retrofitting opportunities at e.g. existing pulp and viscose lines.
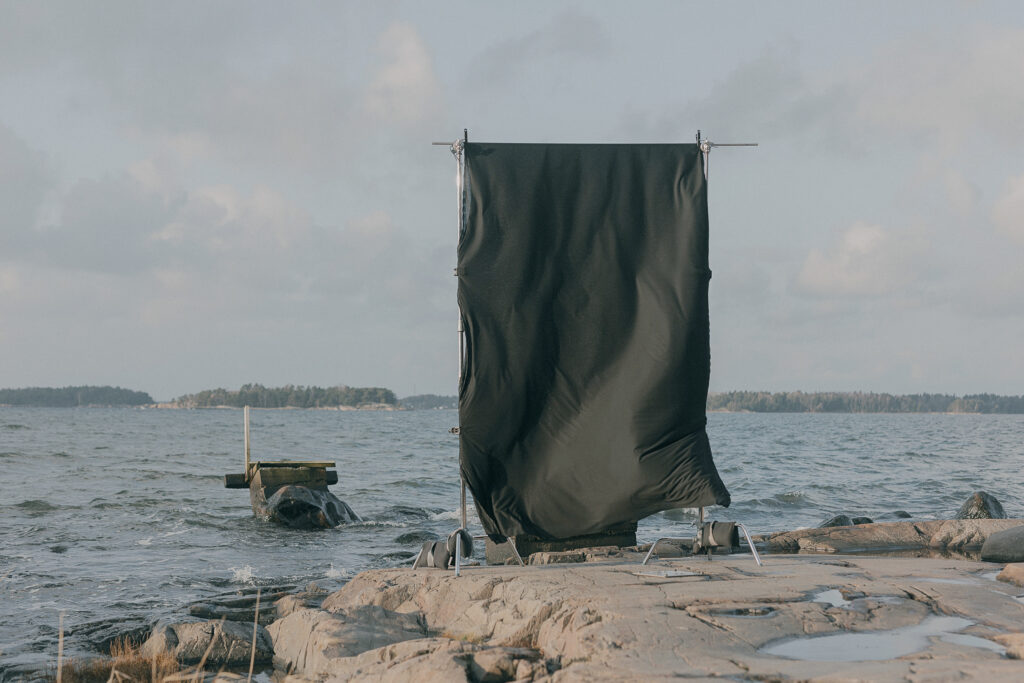
We’re in this together.
Decades of engineering, research and development have brought Infinited Fiber where we are today: ready for our technology to help you meet the growing demand for high-quality regenerated textile fibers.
Real change will happen when we work together. That’s why we offer our partners a simple turnkey factory concept that enables access to a new market. We offer our know-how, clear blueprints and access to top-notch engineering partners to enable the safe delivery and installation of our technology.
Partner with us
Are you a textile waste sorter, a factory equipment engineer, an investor looking for pioneering technology? We’d love to hear from you to discuss opportunities to work together.
For new builds (greenfield)
License our technology and concept blueprint.
Retrofit your existing pulp or viscose factory
License our technology and concept blueprint for converting your existing capacity to cellulose carbamate fiber production.